Each tool adopts different processing parameters for different processing materials. In the field of milling, tool manufacturers develop more targeted coating technologies by optimizing tool materials to improve processing efficiency.
Through the combination of various elements in the material, we can get thousands of raw materials that can be processed. To process these materials, we must know the processing performance of this material and know how to optimize the processing.
The material group that workpeice belongs to:

According to the ISO 531: 1966 international standard, total of 6 major categories of machinable materials are divided into:
Steel material represented by P;
Stainless steel material represented by M;
Cast iron material represented by K;
Non-metallic materials represented by N;
High temperature material represented by S;
High hardness material represented by H;
According to the tensile strength and hardness of the material, tool manufacturers classify materials in smaller categories in these categories. If we cannot find the processing performance parameters of the material to be processed in these small categories, the most feasible way is to consult the tool supplier, I believe they will be happy to help you solve this problem.
Calculation formula
We usually see the following formula in the tool manual
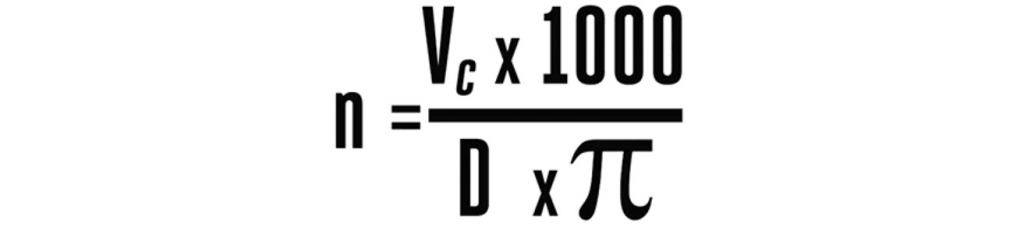
Before talking about this formula, let’s recall that we have learned the formula for the circumference of a circle:
C (Circumference)=π (Circumference Ratio)*d (Diameter)
According to this formula, we can conclude that for a tool with a diameter of D, the distance traveled by the outermost point of the tool for each revolution is: π *D
Then, when the tool rotates at a frequency of n revolutions/1 minute, the distance traveled is: n*π *D
According to the formula of time (T) × speed (V) = distance (S), the speed Vc of the outermost point of the tool at any point in this period of time is: Vc=(n*π *D)/1
The following formula is obtained by conversion: n=Vc/(π *D)
Note! Our cutting tool uses millimeter (mm) as the unit, so the unit of speed Vc in the previous formula is: mm/min
After the length conversion (1m=1000mm), we have this common formula:

After simplifying the equation, we have our final version of the formula:

Note Here! The unit of D (tool diameter) is still mm (millimeter), and the unit of Vc (linear velocity) has become: M/min (meters per minute.)
This formula is also applicable to turning processing, in turning, but the D represents the diameter of the blank.
Of course, the feed and speed calculated by this formula are only for reference. Which feed and speed is the most suitable, needs to be adjusted continuously according to the specific processing environment and conditions